John Arens 9-27-99
- Updated: September 27, 1999
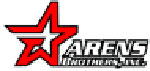
The fact that the sport performance segment of the ATV market is exploding is an extreme understatement! Most racers and extreme rec-riders have selected the Honda Fourtrax 250R as their choice ATV. The problem is that even the newest 250Rs from Honda are now 11 years old! Nowadays finding a used R that’s in decent shape is a real project. Have you noticed all the repair welds on stock 250R frames lately? Long overdue is the availability of a low priced, yet stronger than stock replacement frame. Enter Aren’s Bros. Inc. located in Konler, MI, led by John Arens. Not only does Arens run this full time frame building company. He also is a contributing photojournalist for most of the top selling ATV magazines, Chief editor for the Dist 14 ATV newsletter and he’s the alternative Delegate for District 14. Add the fact that he can be seen at just about every Grand National Championship ATV race, and you can see his involvement with the sport is pretty sincere. Aren’s has kept a well-tuned eye on the sport/performance ATV market for many years, and he’s not afraid to ruffle the feathers of the manufactures to get them more involved with the ATV sport segment. While the manufactures haven’t introduced too many new hi-performance race ready quads, Aren’s has picked up their slack by offering an alternative way to buy a new ATV.
ATV Scene: Hello John. We’ve seen some of the quad parts you’ve been building for a while now, and quite a few people would like to know more about them. First of all, tell us about how you ended up building your own frames.
Arens: Well, I was working for an engineering company, and I wanted an aftermarket frame for my brother and myself. I didn’t really like some of the things that the other companies of the day offered, plus I thought they were overpriced, so I decided to design my own on CAD (Computer Aided Design) and build it as well. After that, people started to find out about it, and it just snowballed from there.
ATV Scene: Ok. Tell us a little about the Honda frames you’re building. Not many people know much about them.
Arens: Right. Well, we first put it on CAD several years ago, and we’ve been building a replacement frame for the Honda Fourtrax 250R for three years now, although that’s not really widely known because we’ve never placed an ad, and we still haven’t. Actually we’ve never needed to! Every frame we’ve ever built has been spoken for before it was actually completed, and it’s still this way. I don’t know if we’ll ever get a supply on hand, but each time we increase the size of the run. It would be nice to have a few extras, but it hasn’t happened so far.
ATV Scene: So what are the details of the frame itself?
Arens: The frame we build is actually a direct replacement for the stock unit, although we’ve cleaned it up quite a bit. We basically evaluated all the components on a stock chassis and either changed and improved the stock design, or eliminated any of the unnecessary stuff that 99% of the riders were getting rid of anyway. The result is a very clean frame design that still retains the essential components to make your stock parts bolt up correctly. Basic geometry is very similar to the 1988/89 Honda 250R, but handling has been improved with a few changes that have been built into our design. Most people can’t see them however, and it’s actually a little difficult to measure them unless you know what to look for. Anyway, we had to follow some areas pretty close to the stock design so everybody’s stock parts would fit. However, we use a different rear brake lever and we don’t use the stock snorkel tube that feeds the airbox. We are working on an alternative for the Cross Country guys for that though.
ATV Scene: What are you using for material?
Arens: We build the frames out of 4130 Chromoly round tubing. This tubing is certified to a military spec, and I feel it has the right characteristics for the end product. It’s an excellent material, and it wouldn’t be certified for aircraft use if it were of questionable value. Chromoly actually has quite a bit of what is known as “memory”; that is, an inherent ability to return to it’s original position and shape after being acted on by an opposing force. In other words, “springback”. This is only to a certain point however! Beyond that, it will want to hold the new form that was acted upon it.
ATV Scene: Everybody says Chromoly is lighter than the mild steel the factories use. Is that true?
Arens: No, not really. Units of measurement are consistent regardless of material, but if you want to know relative material weight, look at the Periodic Table of the Elements. However, the main reason objects built with chromoly end up being quite a bit lighter is that chromoly offers quite a bit more strength per unit than many of the mild materials used in the stock components. The tensile strength of 4130 is far beyond that of most of the mild alloys. As a result, you can use a thinner wall 4130 material and achieve the same or in many cases a better result. In the case of the aftermarket ATV frames being built today, another big factor is that we’re using round tubing instead of square. Remember that the area of a 1″ diameter circle is much less than the area of a 1″ square – over 20% less!
ATV Scene: So what is the weight of your frame?
Arens: Completed unit, which includes subframe, front motor mount and head stay is 39-1/2 pounds. We could have trimmed it down a little more, but the main goal was durability, and as a result some of the frame tubes are thicker than actually needed just as a measure of security. In testing the design we deliberately built some very light units with a much thinner wall material and they held up excellent, but we still increased wall thickness. I got a little bit gun shy! We’re still under any of the stock frames however. All the stock frames seemed to range between 42 and 46 pounds.
ATV Scene: Then why do many of the factories use square tubing?
Arens: It’s MUCH easier for them to process. Think about welding it together. You simply cut or shear the square tubing off at the right location and it will mate up well enough with it’s adjoining part for your robotic wire-feed MIG welder to fill in any gap by ramming in enough wire to get the job done. To top it off, you’ll still be left with either a stub of wire, or a knobby sized blob of weld puddle at one end or the other of the weld. Robotic welders go in straight lines very well, but it is much more difficult to program a robotic welder to go around a round tube and follow a multi-plane contour. Making the joint where a round tube meets a round tube is one of the most difficult and critical operations in making these frames, and the factories aren’t very good at it. Even some of the hottest models today like the 400 EX show this problem. Most of what they do – like merely stamping the tube flat – would be OK for swingsets and weed whackers, but not much else. Off ALL the companies making ATV related stuff these days, I have no doubt we are the masters of making that notch joint for round tubing weldments. This includes all of the factories.
ATV Scene: Really? Sounds like a little bragging John! So what are you doing different than everybody else?
Arens: Yes, I suppose it is in a way, but we’ve spent a tremendous amount of time refining that process, and at this time, we’ve got it pretty well mastered. It’s really because every component on our frame has been designed on CAD, including all of the tube notching. We had to do it that way! Manual tube notching is VERY time consuming, and we simply had to find a better way. As a result, all of our notching is done on a multi axis laser. You wouldn’t believe the time savings. In fact, with this system, we could easily do the notching work for any of the major factories entire model run. You get perfect parts complete with any holes already pierced in them ready for welding, each one identical to the one ahead of it and the thousands behind it. This even includes tubes that have already been bent to their final form. It’s that good! You know, a 1.1 million-dollar laser can really brighten your day!
ATV Scene: So are the other components of the frame cut by laser as well?
Arens: Well, everything is cut either by CNC guided laser or waterjet. Waterjet cutting is actually a very precise and very high pressure – about 60,000 psi – stream of water that cuts extremely well. This can be an advantage in cutting parts that need to be formed (bent) later, because waterjet cutting does not heat the material like some lasers can. When you overheat a material you actually can change its molecular structure, and it changes to a state called “martinsite”, which is a realigning of the molecules. This can sometimes create a brittle spot in the part, and welding can also create these types of conditions if not carefully controlled. That being said, both cutting forms have their place, and we use them both. The only remaining steps are the bending and welding. All the bending is also done on CNC equipment as well, but it has to be.
ATV Scene: Why is that?
Arens: We had to have the bending done to very tight tolerances, because that’s the way our welding fixture is built. Every part had to fit exactly the same. Really, some of the magazines have said the aftermarket companies can’t hold the tolerances the factories do, and actually that is wrong. Aftermarket companies should be able to hold tighter tolerances than the factories. If you need to saw or file or hammer your new frame just to get the motor in, you’ve got the wrong frame builder. That being said, some of the aftermarket companies build stuff that leaves a lot to be desired and I’ve seen parts that won’t fit anything without a lot of work. It’s too bad really, but they control their own stuff. Our benchmark has always been that the stock components WILL fit our frames.
ATV Scene: So that leaves the welding?
Arens: Right. We TIG weld everything, and technicians certified by the FAA for aircraft work do all our welding. In fact, one guy was certified for nuclear work by the US Navy. He actually worked on the reactor compartment components in the Trident and Seawolf Class nuclear subs for the Navy. I think he’s more than capable of handling some ATV stuff, but they all are.
ATV Scene: I would think so. If I ever get that home reactor project going, I’ll give him a call. (The Fusion Buddy!) Anyway, is everything powder coated after that?
Arens: Yes. Powder coating is very durable, and everything gets powder coated unless the rider wants it bare to put on his or her own special color. I try to stick to only a few different colors though. Trying to match a color for somebody can get you into trouble. After that, the subframe is fastened inside the main frame, by the way, the subframes are obviously removable, the new one-piece front motor mount is added along with the new head stay, and the job is done. Then it’s just a matter of wrapping it up and sending it off!
ATV Scene: So how have your frames held up in the past?
Arens: Actually they’ve held up extremely well. In fact, CT Racing just ran one in a 24-hour desert race. After slamming rocks and bumps at high speed for 24 hours under 5 different riders, we had no cracks. That’s not to say they are completely indestructible though. Our frames are a competition-designed unit, and someday, somebody will probably break one. A big factor in the desert was that Alan Knowles at CT Racing is extremely good at setting up suspension. Suspension setup is critical in taking up the force transmitted to the ATV frame. Constant bottoming will destroy any frame. As for your question though, they’ve held up extremely well.
ATV Scene: Now the big question. What about price?
Arens: Well this is actually a good question for us. Since so much of the process is automated, we are able to keep the price quite low compared to any other aftermarket company. We’ve been selling these frames for a little under $1500, which is usually about a thousand dollars less than the other guys have!
ATV Scene: Really! So what other quad stuff are you doing?
Arens: Well we’re building some swingarms for 250R’s and starting some for the 400EX, along with steering stems and A-arms for both. If we ever get time, we’ll carry it over into a few other models as well. By the way, these parts are all built with the same materials and processes, and once again we try to keep the price reasonable. Also we have been testing a new quad frame design for the Yamaha YZ 400 dirt bike motor. We have built a couple and they turned out excellent! We will have that frame available to the public shortly.
ATV Scene: So how does somebody get one of your frames or the other stuff you build?
Arens: They just have to give me a call, and we’ll try to help them out! My shop number is 517-593-2599 and my email address is jarens@voyager.net. I’ve also got a guy working on a web site, and hopefully that will be ready soon.